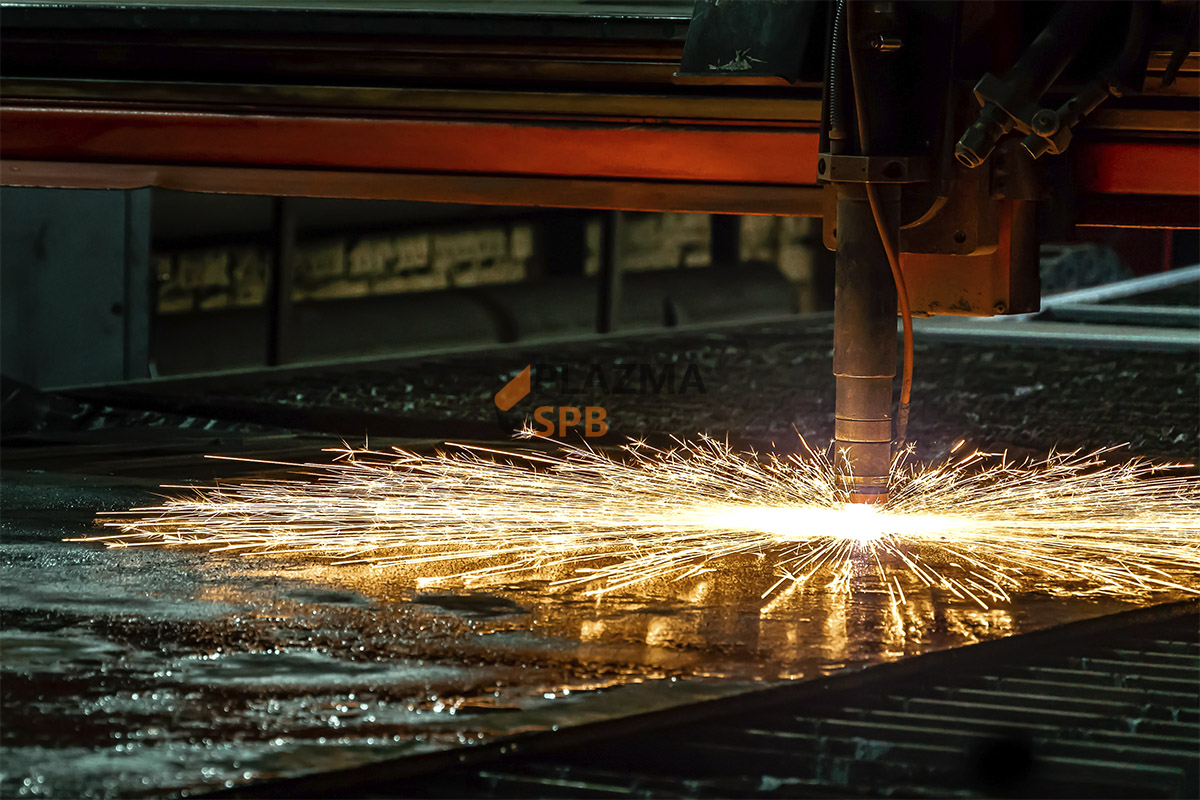
Лазер широко применяется в промышленности, поскольку обеспечивает точный и качественный раскрой заготовок. Однако при резке толстого металла возникают трудности. Их легко избежать, если тщательно соблюдать технологию резки и учитывать особенности сплава.
Принцип лазерной резки
Лазерный луч фокусируется в заданной точке и нагревает металл. В результате лазер плавит и испаряет его, осуществляя рез. В операции также задействован газ — он охлаждает и очищает зону реза.
Лазерная обработка производится на специальных станках. Они генерируют луч при помощи источника энергии и усиливают его, пропуская через оптическую систему. Лазерные установки бывают двух видов:
- Твердотельные. В таких станках источником энергии выступает импульсная лампа, а рабочее тело выполняется из кристаллов и редкоземельных элементов.
- Газовые. В таких станках активная среда представлена газом. Он возбуждается электрическим разрядом и ионизируется. В результате генерируется лазерное излучение.
Лазер обеспечивает точный и чистый рез, поскольку станки оснащаются системами с ЧПУ — числовым программным управлением. Оно автоматизирует процесс: станок многократно повторяет заданные операции и не отклоняется от контура резки. Благодаря автоматизации повышается эффективность производства.
Сложности резки толстого металла
При лазерной резке толстого металла возникают различные трудности. Раскрой занимает больше времени и требует повышения мощности лазера. Растут энергозатраты, а оптическая система станка быстрее засоряется.
Помимо этого на поверхности металла нередко возникают дефекты. Риск их появления во многом зависит от физико-химических характеристик сплава:
- При резке холоднокатаных листов с низким содержанием углерода края реза размягчаются. Поэтому металлу потребуется дополнительная обработка: закалка для возврата прочности и отпуск для снятия внутренних напряжений.
- При резке листов с высоким содержанием углерода края реза закаляются. Поэтому при дальнейшей обработке металла возрастает риск появления микротрещин и разрушения структуры материала.
Избежать появления дефектов помогает тщательная настройка оборудования. Режим резки оптимизируется под характеристиками сплава.
Наиболее распространенные дефекты
Дефекты часто появляются из-за ошибок в технологии резки или низкого качества металла. Еще одна причина — ненадлежащее обслуживание оборудования и неисправности в его конструкции. К самым распространенным дефектам металла относятся:
- Грат. Капли расплавленного металла затвердевают на кромках изделия. Грат возникает при нарушении скорости резки. Устраняется шлифовкой.
- Неровный срез. Проблема связана с конструкцией лазерной установки. При нарушении режущего угла лазерный луч отклоняется, и края среза получаются неровными.
- Вихри и борозды. Зона реза охлаждается и очищается при помощи газа. Если газовый поток воздействует на металл вне зоны реза, возникают вихри и борозды. Проблема связана с неправильной установкой газового резака, недостаточным давлением или скоростью подачи газа.
- Термическая деформация. Неравномерный нагрев материала при использовании лазерного луча приводит к деформации заготовки. Нарушение размера и контура резки приводит к проблемам при сборке конечного изделия. Проблема решается регулировкой скорости и мощности лазерного луча и охлаждением зоны реза.
- Окисление. Металл окисляется под воздействием высокой температуры, и на краях среза возникают оксидные пятна. Проблема решается применением охлаждающего газа и дополнительной обработкой поверхности.
Оставляйте заявку прямо сейчас и получите подробную консультацию с расчетом стоимости проекта от раскроя металла до монтажа готовой конструкции
Оставить заявку