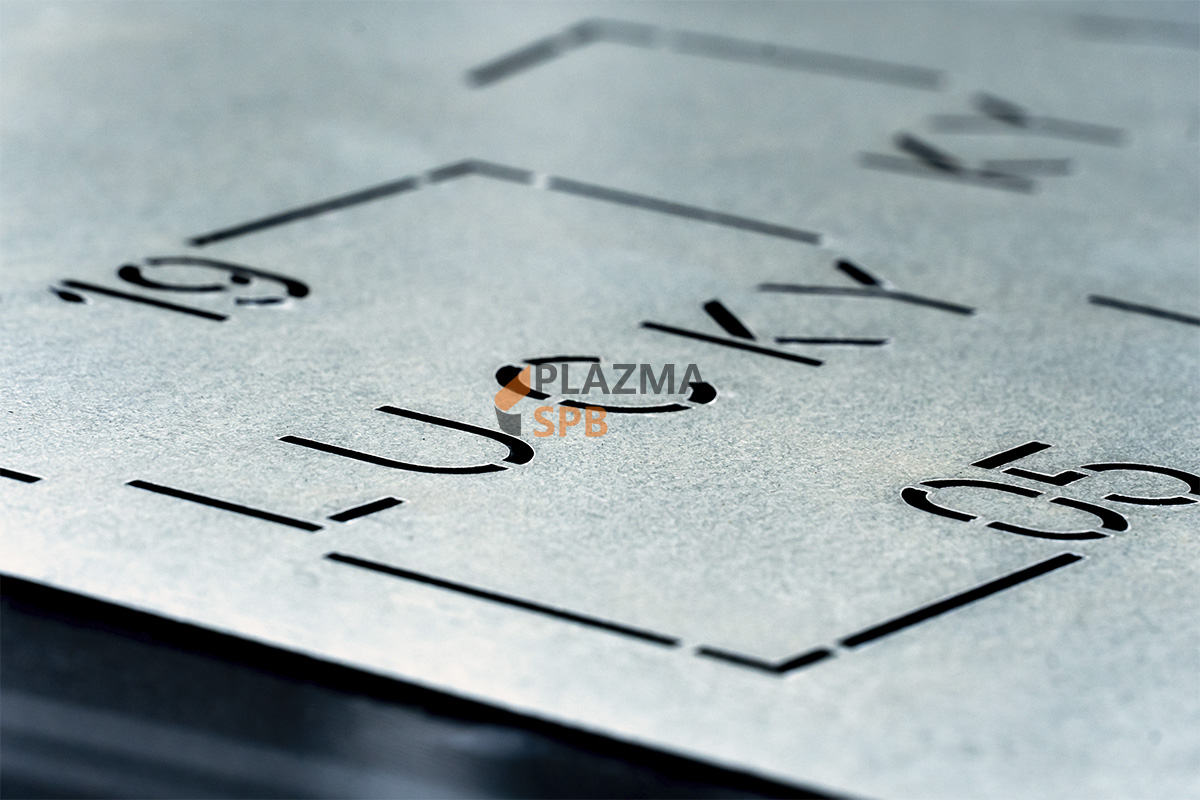
Лазерная резка металла — высокотехнологичная операция по металлообработке, применяющаяся для изготовления деталей аппаратуры особой точности и обеспечивающих безопасность элементов металлоконструкций. Цена ошибок и брака в таких производствах чрезвычайно высока.
Даже в тех случаях, когда скрупулезное соблюдение геометрии при резке не столь значимо, поверхностные дефекты могут негативно сказаться на качестве и внешнем виде изделий. Небольшие погрешности устраняются дополнительной обработкой, но это требует временных и материальных затрат.
При грамотном подходе и профилактике дефектов можно избежать вовсе или свести риск их появления к минимуму.
Причины возникновения дефектов
В целом, причиной ошибок при лазерной резке является нарушение технологических требований. Лазерная резка относится к термическим способам обработки металла, и температурный режим должен соответствовать свойствам металла и параметрам заготовки. Режущим агентом выступает лазерный луч, фокусируемый линзой на поверхности металла. От точности фокусировки зависит ширина реза и четкость кромок. Излишки расплава металла удаляются потоком сжатого газа, и для чистоты реза необходимо тщательно контролировать его давление.
Источником некорректной работы лазерного оборудования, вызывающей дефекты обработки, могут быть как технические сбои, так и человеческий фактор. Наиболее частые причины таковы:
- Некачественный материал заготовок;
- Незнание физико-механических свойств обрабатываемого металла;
- Недостаточно подготовленные специалисты;
- Небрежное техническое обслуживание оборудования и загрязнение линз и рабочего стола;
- Неверная наладка операций, неправильный выбор мощности, скорости, давления газа, фокусировки лазерного пучка;
- Использование неподходящей газовой среды;
- Плохо закрепленные на рабочем столе заготовки.
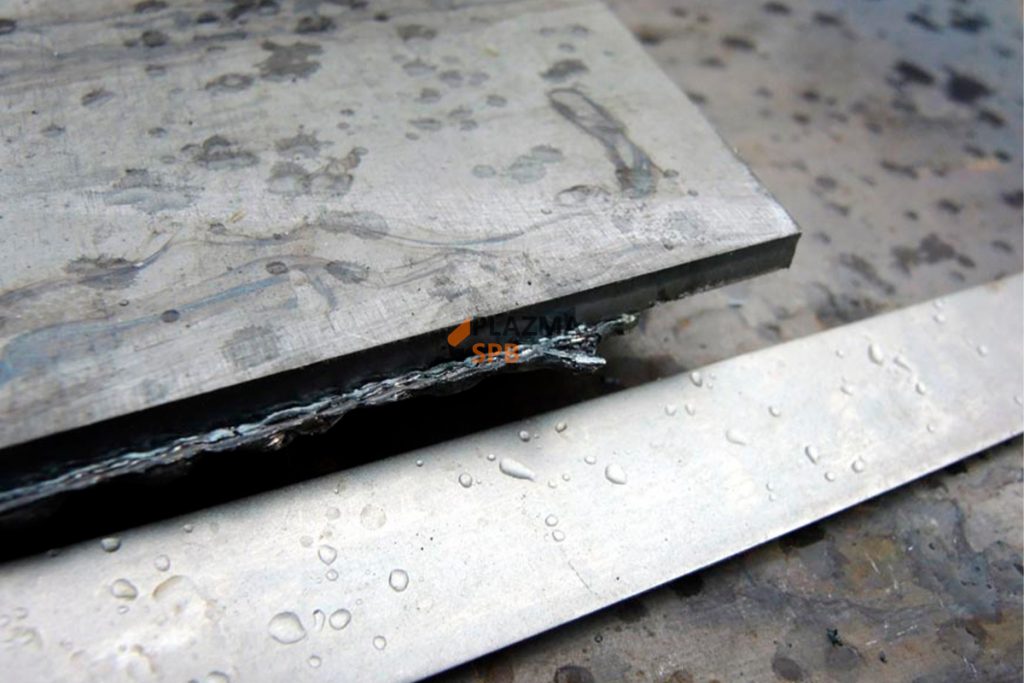
Возможные дефекты при лазерной резке и их профилактика
Перечисленные выше погрешности в подготовке и организации процесса лазерной резки приводят к образованию типичных дефектов, которые можно обнаружить на поверхности и кромках деталей. Они могут затрагивать физические свойства металла, изменять заданные размеры и внешний вид.
Окалина. Слой окислов металла, образующийся при высокой температуре в присутствии кислорода. Чем дольше металл подвергается термическому воздействию, тем толще слой окалины. Для предотвращения появления окалины нужно следить, чтобы не замедлялась скорость резки, а температура не поднималась выше функционально необходимых значений. Чтобы окислы не оседали на поверхности кромки, в место контакта лазера с заготовкой подается струя сжатого газа, который выдувает окислы из зоны реза. Эффективно также создание бескислородной среды с использованием азота или инертных газов.
Грат. Застывшие частицы металлического расплава, прилипшие к кромке. Чаще всего образуется при слишком высокой скорости резки. На образование грата также влияет нарушение фокусировки луча: при завышенном фокусе расплав оседает в виде бисерных капель с уходящими вниз по кромке желобками, а при слишком низко расположенной точке фокусировки грат похож на крошку и сопровождается выбоинами на поверхности. Избегать образования и налипания грата позволяет точность фокусировки и снижение скорости подачи заготовки при первых признаках брака.
Ребристость, заусенцы, гребешки на кромке реза возникают, когда установка работает со слишком высокими параметрами скорости, мощности и давления газа. Точная настройка оборудования по толщине заготовки и физико-механическим характеристикам металла, а также постоянный контроль в ходе резки обеспечивают гладкие кромки. Причиной подобных дефектов может стать засорение сопла лазерной головки или загрязнение линзы, поэтому важно проводить регулярное техническое обслуживание станка.
Вихри и борозды на поверхности кромки могут образоваться при резке металла большой толщины при сбоях в подаче вспомогательного газа. Для профилактики подобных недочетов необходим постоянный контроль за давлением газа и проверка редуктора в целях предотвращения засорения.
Нарушение ширины реза. Чувствительный недостаток, ведь лазерную резку часто выбирают именно за возможность реза толщиной в десятые доли миллиметра. Рез может получиться шире заданного в результате нарушения фокусировки, поэтому фокусирующая головка нуждается в постоянной калибровке и профилактическом обслуживании. Точность настройки фокуса также зависит от аккуратности и профессионализма оператора станка.
Неровный рез. Как правило, неровный рез — следствие плохой фиксации заготовки на рабочем столе или износа механики станка с лазерной установкой. Тщательное закрепление детали перед обработкой, наладка, своевременный ремонт и замена выработавших ресурс деталей — залог получения ровного качественного реза.
Перегрев стали с образованием крупнозернистой структуры, повышающей хрупкость металла. Чтобы температуры не достигали критических значений, необходима регулировка мощности лазера с поддержанием нагрева в допустимом диапазоне.
Для получения запланированного результата лазерной резки нужно использовать надежное оборудование и строго соблюдать технологию.
Размещать заказы рекомендуется в компании с многолетним опытом, имеющей современное содержащееся в порядке оснащение и располагающей квалифицированными специалистами по наладке и эксплуатации станков с лазерными установками.
Оставляйте заявку прямо сейчас и получите подробную консультацию с расчетом стоимости проекта от раскроя металла до монтажа готовой конструкции
Оставить заявку