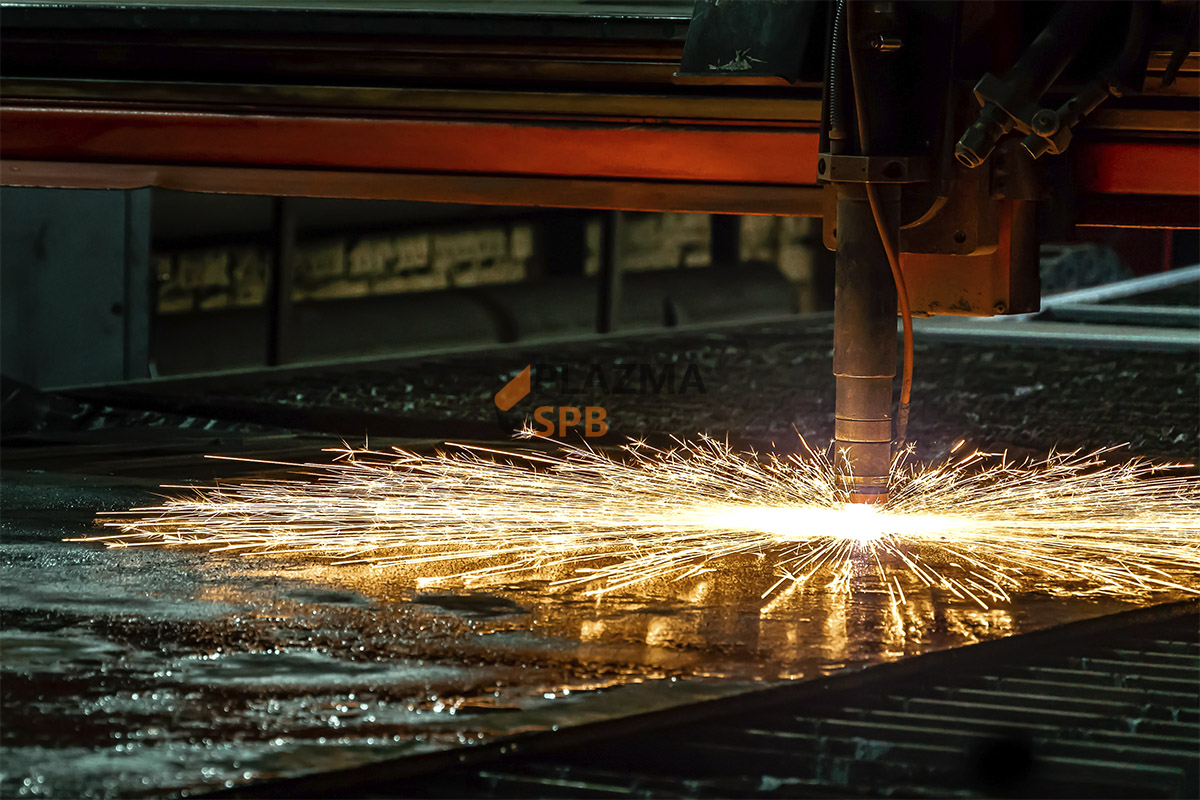
Современные технологии призваны значительно упрощать жизнь человека. Сегодня уже трудно представить промышленность без станков и программного обеспечения, производства без функционального оборудования.
Вот и в сфере обработки листового металла существуют множество востребованных и конкурирующих между собой технологий. В частности плазменная и газокислородная резка.
Пламя и плазма
Газокислородная резка представляет собой струю кислорода, которая способна с помощью горючих газов сжигать металл. Плазма же – это ионизированный газ, раскалённый настолько, что меняет свои свойства и позволяет прожигать даже тугоплавкие металлические поверхности.
Обе технологии используются для резки металлических листов, потому что способны направленно и точно следуя заданной программе разрезать металл, разогревая его до сверхвысоких температур.
В чём же различия газокислородной и плазменной резки? Какие плюсы и минусы имеют эти технологии? И почему плазменный способ обработки металла постепенно вытесняет газокислородный? На эти вопросы мы постарались дать ответы в этой статье.
Газокислородная резка: принципы работы, преимущества и недостатки
Газокислородная резка – традиционный способ обработки листовых металлов, давно используемый в промышленности. В последние годы этот тип резки всё активнее теряет свои позиции под давлением более прогрессивных способов резки.
Технология резки газом основывается на том, что горящий газ предварительно нагревает поверхность металла до температуры плавления, а струя воспламенившегося кислорода прожигает эту поверхность, попутно выдувая шлак из пропила.
К главным достоинствам газокислородной резки можно отнести:
- Возможность работы с металлическими листами высокой толщины. Газокислородная система может резать металл толщиной более 30 см.
- Сферы применения. Можно выполнять резку, нагревание, пайку или сварку.
- Относительно низкая стоимость оборудования.
- Подходит для резки в полевых условиях. Существуют портативные системы резки, которые обеспечивают высокую степень мобильности, поскольку не нуждаются в электроэнергии.
К недостаткам способа относят:
- Подходит не для всех материалов. Газокислородная резка обычно применяется в обработке углеродистой стали и чёрных металлов, содержащих железо.
- Низкая скорость работы.
- Высокий риск появления на поверхности металла окалин. При плазменной обработке риск так же присутствует, но в этом случае, окалина легко удаляется с поверхности.
- Низкое качество обработки тонких листов материала.
- Необходимость чёткого соблюдения правил безопасности в работе. Газокислородная резка предполагает использование нестабильных горючих газов, поэтому в производстве следует неукоснительно соблюдать нормативы работы с таким оборудованием.
- Периодические затраты на покупку газа.
Плазменная резка: технология применения и характеристики
При плазменном способе резки используется ионизированный газ, который проводит электричество – проще говоря, плазма. Чем больше электроэнергии проходит через дугу плазмы, тем больше она нагревается, что позволяет ей приобрести высокую режущую способность.
Плазменная резка обладает высокой эффективностью и работоспособностью. В современной промышленности всё активнее применяется этот способ обработки листового металла.
Рассмотрим подробнее преимущества плазменных станков:
- Плазменные станки способны работать даже с листами высокой толщины, до 36 мм. Однако наилучший результат плазменный способ обработки металла показывает в работе с тонким металлом.
- Универсальность материалов для работы. Плазма используется при обработке таких материалов, как:
- углеродистая и легированная сталь (толщиной до 150 миллиметров);
- медь (толщиной до 80 миллиметров);
- алюминий и его сплавы (толщиной до 120 миллиметров);
- чугун (толщиной до 90 миллиметров).
- Высокая скорость работы. Плазменная резка в основном не требует последующей обработки шва, следовательно, экономия времени превращается в экономию средств на производстве.
- Относительная безопасность работы с плазменными станками. Технология достаточно простая, и не предполагает работу с легковоспламеняющимися веществами.
- Точность раскройки. Плазменный поток обеспечивает более узкий и гладкий рез без шлака.
Также плазменный способ обработки обладает и определёнными минусами:
- Низкая мобильность. Плазменные системы имеют потребность в источнике сжатого воздуха и электроэнергии.
- Конусность отверстия. В случае, если аккуратность вырезанных отверстий имеет большую значимость при обработке конкретной заготовки, важно учитывать, что плазма имеет такую особенность, как отклонение дуги по вертикали. Нижнее отверстие при плазменной резке получается уже верхнего. Разница возрастает по мере возрастания толщины обрабатываемого листа металла.
- Стоимость работы на плазменном станке увеличивается пропорционально количеству отверстий на одной заготовке. Расходные материалы, применяемые в плазменной резке, рассчитаны на определённое количество циклов включений и выключений.
- Необходимость в сухом воздухе. При попадании влажного воздуха в сопло плазменной системы, есть существенная вероятность снижения качества работы аппарата.
Сравнительный анализ плазменного и газокислородного способов резки
Для подведения итогов необходимо провести сравнение этих двух технологий обработки листового металла. При выборе способа резки нужно понимать, какой и для каких целей оптимально подойдёт. Для качественного результата и плазменный, и газовый методы нужно использовать по назначению.
Однако предыдущие пункты всё же показывают преимущество плазменной резки металла перед газокислородной. Сравним:
- Процесс резки. Технология плазменной резки значительно легче технологии газовой: не требуется предварительное нагревание материала, определённая квалификация сотрудника не имеет критического значения, а качество резки не зависит от множества показателей, как при резке газом.
- Безопасность работы. При обработке с помощью газокислородной резки выделяется горючий газ и вредный шлак, чего не происходит при работе с плазмой.
- Универсальность. Плазменные станки работают с различными видами металлов – сталь, медь, нержавеющая сталь, чугун и другие сплавы, в то время как газокислородный метод резки ограничен некоторыми видами материалов.
- Качество резки. Газокислородный способ резки по данному показателю явно уступает плазменному. Окалины, шлак и неровная поверхность – вот ключевые недостатки системы газовой обработки металлических листов.
- Скорость работы. Плазменная резка быстрее газовой, как минимум, в два раза. Если учитывать, что толщина большей части листового металлопроката составляет менее 30 мм., эффективность плазмы возрастает во много раз.
- Толщина резки. В данном параметре важно то, что с металлопрокатом высокой толщины (от 36 мм.) газовое оборудование справляется гораздо лучше, а вот тонкие листы качественнее режет поток плазмы.
- Экономичность. Стоимость газокислородных станков значительно меньше стоимости плазменных, однако, в процессе эксплуатации, требуется постоянная закупка газа. В плазменных резаках же лишь докупаются расходные материалы. Также, резка газом подразумевает большие временные затраты, нежели плазменная резка – предварительный нагрев материала, непосредственно процесс обработки и доработка среза.
Очевидно, что не существует «хорошей» или «плохой» технологии обработки материалов. Каждый способ целесообразен в определённых условиях и работает в необходимых производственных целях. Поэтому выбирать технологию нужно исходя из таких показателей, как: толщина, вид металла, требуемое качество реза, тип заготовки и финансовая составляющая производства.
Оставляйте заявку прямо сейчас и получите подробную консультацию с расчетом стоимости проекта от раскроя металла до монтажа готовой конструкции
Оставить заявку