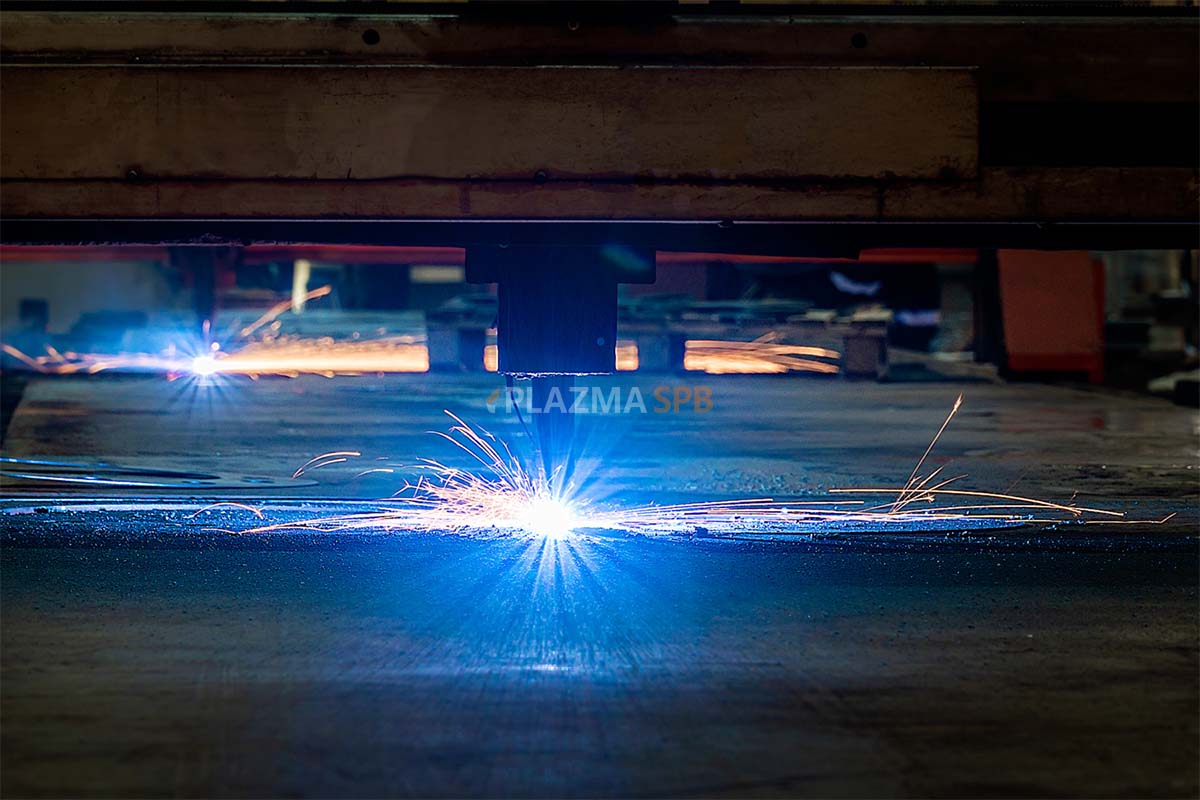
Лазерная резка материалов — это популярная и востребованная технология. Лазер обеспечивает точный и качественный рез по контуру. Для обработки металлов используются более мощные лазерные станки, чем для других материалов. Чтобы выбрать подходящую модель станка, следует разобраться в их видах и конструктивных особенностях.
Виды лазерных станков
Лазер нагревает металл в узкой области. Под воздействием высокой температуры металл плавится и испаряется. В рабочую зону подается газ или кислород, который выдувает отходы и охлаждает кромки реза. Для лазерной резки используются специальные станки:
- Газовые. Лазерное излучение вырабатывается в газовой среде, которая возбуждается и ионизируется при помощи электрического разряда. Луч проходит через оптическую систему, усиливается и направляется к поверхности металла.
- Твердотельные. Лазер генерируется импульсной лампой, проходит через оптическую систему и осуществляет рез. Рабочее тело – цилиндрический стержень – станка выполняется из кристалла или легированного стекла.
- Оптоволоконные. Подвид твердотельных лазеров, но более универсальный. Они дают возможность работать с различными металлами и сплавами: черными, цветными и ферросплавами. В оптоволоконных станках лазерной средой и резонатором выступает оптоволокно. В оптоволоконный кабель накачивается свет, который усиливается благодаря высокому показателю преломления.
Обслуживание и электропотребление станка влияет на конечную стоимость лазерной резки. При выборе модели следует исходить из спецификаций проекта. Для резки тонких листов (до 5 мм) достаточно простого лазера с мощностью до 500 ватт. Более мощный невыгодным вложением.
Как выбрать лазерный станок для резки металла
Выбор станка напрямую зависит от задач производства. Параметры и габариты модели должны отвечать объему материала и размерам производственной площадки. При выборе следует обратить внимание на отдельные компоненты станка.
Станина. Основная часть станка, на которой закрепляются все подвижные и неподвижные элементы. Жесткость станины влияет на точность лазерной обработки. Если станине ее не достает, то во время движения резака возникает вибрация. Она приводит к отклонению от контура и деформации заготовки. Вибрации также ускоряет амортизацию станка.
Лазерный источник. Мощность станка зависит от лазерного источника и варьируется от 500 до 120 000 ватт. Некоторые источники оснащаются защитой от выгорания при отражении луча, которая необходима для обработки цветных металлов — титана, алюминия и меди.
Услуги лазерной резки металла предлагают многие производители. Их специалисты подбирают мощность в зависимости от свойств металла и толщины заготовки. Для резки нержавеющей стали толщиной 4-5 мм требуется минимум 1 кВт, а для листа алюминия в 4-5 мм — 1,5 кВт. Для чёрной углеродистой стали толщиной в 10 мм используется мощность в 1 кВт, а для медного листа в 10 мм — 6 кВт.
Лазерная голова. Отвечает за регулировку фокусного расстояния лазерного луча. Фокусное расстояние настраивается под толщину заготовки – автоматически во время или вручную до начала обработки.
Ручная настройка используются для станков с мощностью до 3,3 кВт, которые обрабатывают тонкие металлические листы (до 5-6 мм). Для резки толстых металлов следует выбрать модель станка с автоматической настройкой фокусного расстояния. Резка толстых металлов занимает больше времени, но автоматическая настройка ускорит выполнение операции.
Дополнительное оборудование. Дополнительные устройства продаются в комплекте со станком. Они повышают производительность и делают рабочий процесс более удобным. К дополнительному оборудованию относятся чиллеры, стабилизаторы напряжения, компрессоры и газификаторы и система вытяжки.
Чиллер используется для охлаждения лазерного излучателя и лазерной головы. Стабилизаторы поддерживают стабильное напряжение, компрессоры и газификаторы применяются для подачи кислорода и газа. Система вытяжки предотвращает загрязнение воздуха в рабочем помещении.
Оставляйте заявку прямо сейчас и получите подробную консультацию с расчетом стоимости проекта от раскроя металла до монтажа готовой конструкции
Оставить заявку