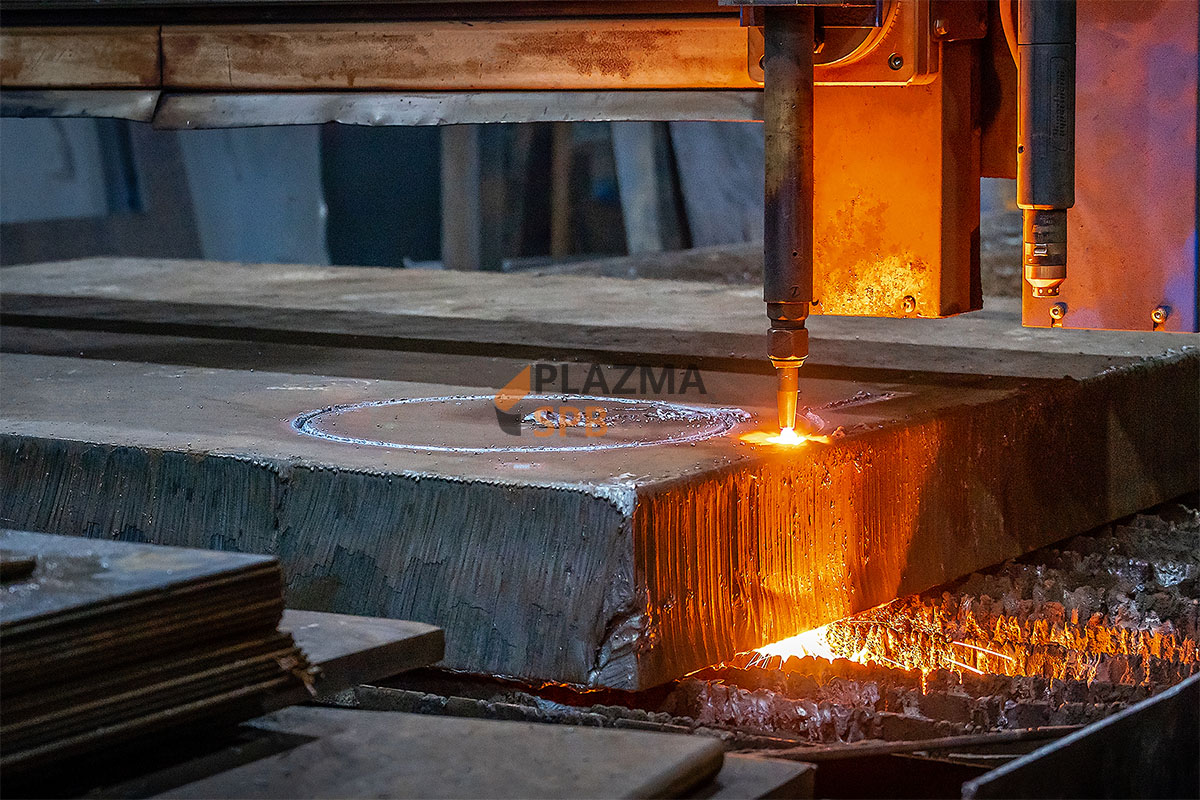
Газовая резка — одна из наиболее распространенных технологий термической обработки металла. Она приобрела популярность благодаря простоте: для работы не требуется дорогостоящее оборудование и дополнительные источники энергии. В этом материале рассмотрим принцип газовой резки и его особенности.
Принцип технологии газовой резки
В процессе газовой резки на поверхность металла направляется струя кислорода, которая под давлением смешивается с горючим газом и затем поджигается. В результате воспламененная газовая струя нагревает и плавит металл.
В качестве горючего газа применяется ацетилен, пропан-бутановая смесь или натуральный природный газ. Выбор обусловлен конкретными условиями обработки — например, для резки под водой используются пары керосина.
Газовая резка в том числе осуществляется на станках с ЧПУ. В соответствии с программой резак перемещается по заданному контуру, направляя на поверхность металла воспламененную струю газа. Интенсивное горение металла происходит только в верхних слоях металла, поскольку газовая струя не проникает достаточно глубоко. Дальнейший нагрев происходит уже за счет горения самого металла и тепла, которое выделяется в процессе.
Газовая струя не только поджигает металл, но и выполняет другие функции: создает защитную среду вокруг зоны реза и не допускает проникновение азота, а также компенсирует потери тепла при резке металлов с высоким показателем теплопроводности.
Во время газовой резки необходимо соблюдать несколько условий, чтобы обеспечить качественный результат:
- температура горения металла под струей газа должна быть ниже температуры плавления, чтобы металл воспламенился раньше, чем перейдет в жидкое состояние;
- окислы удаляются путем плавления при температуре ниже, чем температура горения металла. Если снизить температуру не получается, то в процессе газовой резки применяются специальный флюсы — вещества, которые защищают металл от окисления;
- высокая теплопроводность металла затрудняет или полностью прерывает газовую резку, поэтому технология оптимальна для резки сталей с малым или средним содержанием углерода.
Виды газовой резки
Газовая резка востребована в промышленности, поскольку дает возможность обрабатывать металлы различной толщины и состава. При этом технология считается недорогой и простой в исполнении.
Однако имеются некоторые ограничения для ее применения при резке углеродистых сталей. В основном, газовая резка используется для обработки сталей, в которых содержится 0,3-0,5% углерода. Если показатель достигает 0,8%, поверхность стали необходимо предварительно нагревать до 300 °С, из-за чего повышается риск появления трещин. При более высоком содержании углерода (от 0,8%) сталь предварительно нагревается до 400 °С.
Выделяется несколько способов газовой резки:
- Кислородно-флюсовая. Используется для резки высоколегированных, нержавеющих и хромоникелевых сталей. При этом металл покрывается флюсом – веществом, которое защищает металл от окисления;
- Газо-дуговая. Способ отличает применение «скользящей» электрической дуги, которая образуется между электродом и поверхностью металла. С помощью этой дуги металл нагревается до температуры плавления.
- Подводная. Для подводной резки применяются водородно-кислородные резаки, которые дают возможность раскроить металл толщиной до 75 мм на глубине до 30 метров.
При газовой резке металла применяются различные виды резаков. Для ручной резки используются ацетиленовые резаки с щелевыми и многосопловыми мундштуками.
Если резка осуществляется на станке, резак устанавливается на опорную каретку и движется вдоль линии реза. Автоматизация процесса дает более качественный рез, потому что резак не колеблется и сходит с заданного контура.
Оставляйте заявку прямо сейчас и получите подробную консультацию с расчетом стоимости проекта от раскроя металла до монтажа готовой конструкции
Оставить заявку