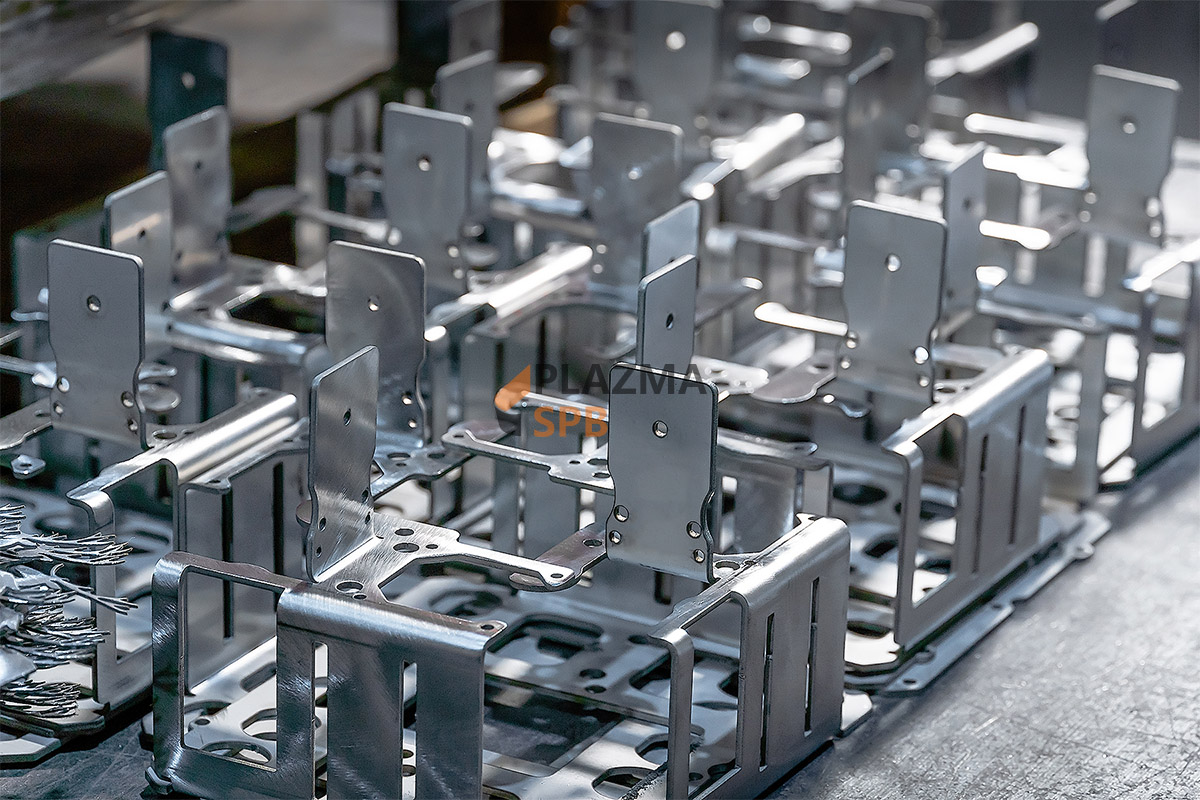
Для получения в металле отверстий необходимой формы часто прибегают к такому процессу как «координатная пробивка металла». В зависимости от толщины стали, геометрической формы отверстия, точности его расположения используются ручные инструменты или токарные станки с цифровым программным управлением. Координатная пробивка позволяет создать в заготовке за один проход множество отверстий – матрицу, что существенно экономит время и трудовые резервы.
Какое оборудование применяется для координатной пробивки, в каких отраслях промышленности она используется, как выглядит сам процесс с точки зрения технологии: об этом в материале статьи.
Суть координатной пробивки
Пробивка металла по заданным координатам – это один из способов холодной обработки металлов. В результате мощного и динамичного импульса энергии, передаваемого рабочим инструментом станка, в металле получатся отверстия чёткой геометрической формы. Чаще всего в качестве исполнительного механизма применяется пуансон с заданной матрицей. За счёт ударной нагрузки происходит разрушение кристаллической решётки сплава металла без его деформации.
При средне- и крупносерийном производстве изделий координатная пробивка выполняется на станках с ЧПУ. Они позволяют спозиционировать отверстие с точностью до 0,001 мм и исключить влияние «человеческого фактора». Это очень важно при автоматизированном производстве, когда оператор лишь наблюдает за бесперебойностью работы оборудования. Станки с ЧПУ обладают интеллектуальным программным обеспечением, дающим возможность быстро составить алгоритм работы и запустить детали в производство.
Оборудование для координатной пробивки
Станки, используемые для пробивки отверстий в металле, условно подразделяются на две крупных категории:
- с ручным управлением или полуавтоматические;
- автоматические.
В качестве исполнительных элементов используются пробойники и штампы.
К первой группе оборудования относятся станки и прессы с механическим, гидравлическим или электрическим приводом.Во вторую группу входят автоматизированные станки с ЧПУ, не требующие участия оператора в процессе. К ним принято относить координатно-пробивные прессы и координатно-пробивные машины.
Автоматическое оборудование постепенно заменяет морально устаревшие станки с ручным управлением и гидростанциями. Этому есть ряд объективных причин.
Автоматические координатно-пробивные станки и машины:
- представляют собой многофункциональное оборудование с возможностью быстрой переналадки;
- обладают производительностью, в 50-60 раз превышающей ручное механизированное оборудование;
- имеют простую и понятную систему управления;
- способны выполнять производственные задачи с высокой точностью и без брака.
Основные характеристики координатно-пробивочного оборудования
Чем толще и прочнее металл, чем выше производственные объёмы, тем мощнее должен быть станок или пресс. Базовыми параметрами любой координатно-пробивочной машины являются максимальное рабочее усилие и размеры стола. Именно от них зависит производительность, сроки изготовления изделий, технологичность и ритмичность любого производства.
Кроме того, оборудование различается:
- максимальными размерами обрабатываемого листа металла;
- максимальным диаметром пуансона;
- величиной рабочего хода по осям Х и Y;
- скоростью перемещения заготовки;
- предельной производительностью, измеряемой в ударах/мин;
- мощностью и типом привода;
- типом системы управления.
Большинство современных координатно-пробивочных станков способны работать с матрицами, пуансонами, пробойниками и съёмниками различных геометрических размеров и сечения.
Сфера применения координатной пробивки металла
Координатная пробивка используется практически во всех отраслях промышленности и производства. Но технология особо востребована при производстве различных металлоконструкций и малых архитектурных форм.
В частности, координатную пробивку применяют при изготовлении элементов для:
- витрин и ограждений;
- строительных опор;
- рекламных конструкций щитового типа;
- стеллажей складов и терминалов.
Для нестандартных изделий штампы изготавливаются индивидуально с применением технологии 3D-моделирования.
Оставляйте заявку прямо сейчас и получите подробную консультацию с расчетом стоимости проекта от раскроя металла до монтажа готовой конструкции
Оставить заявку