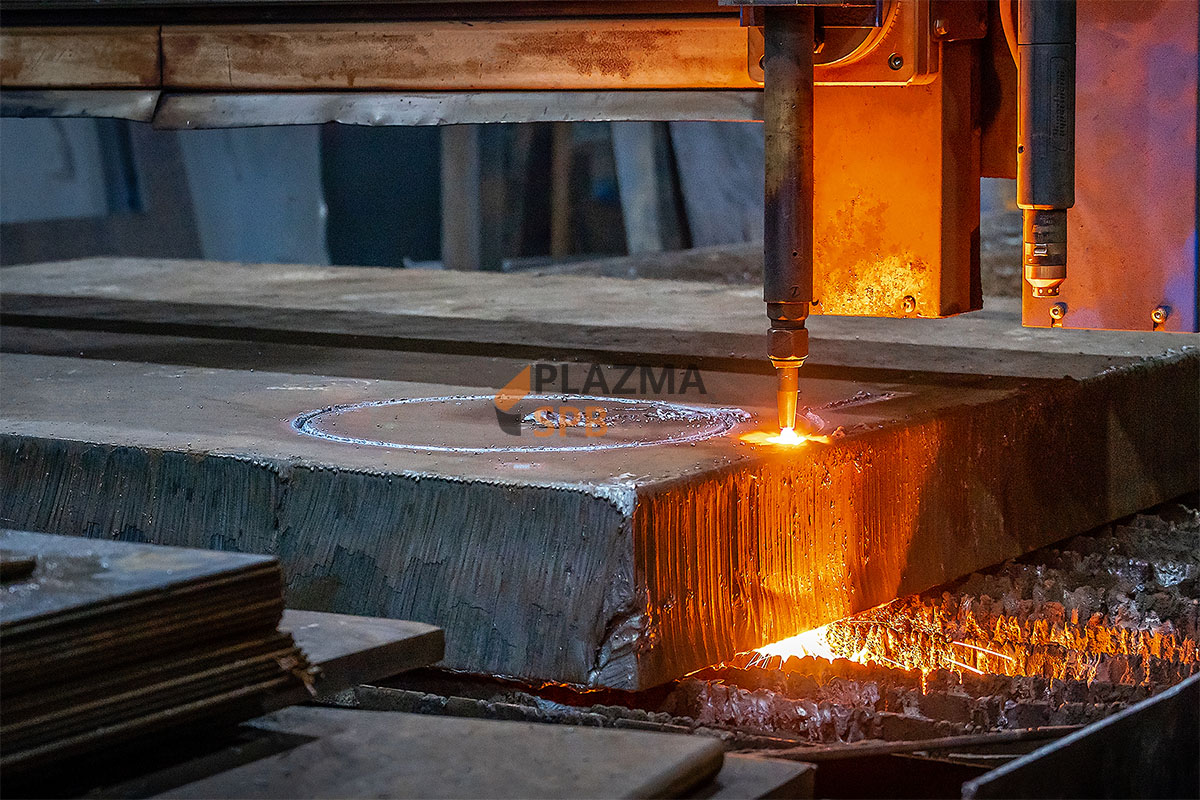
Плазменная резка – быстрый, высокоточный и экономичный способ обработки металлов из всех существующих. Оборудование для плазменной резки обеспечивает погрешность в пределах 0,001 мм. Станки с ручным приводом имеют погрешность до 0,5 мм и более. При обработке металла имеет значение буквально всё: и тип станка, и марка фокусной головки, и размеры рабочего стола, и рабочий ход по осям X и Y, и скорость обработки. Немаловажным фактором качественного раскроя металла является и газ.
Зачем нужен газ для лазерной резки
Суть лазерной обработки металла заключается не только в его расплавлении по контуру будущего изделия, но и удаления расплава с кромок. Разрезание металла обеспечивается лазерным лучом, исходящим из головки, а удаление раскалённых брызг именно газом.
Газ защищает зону резки от воздействия кислорода, влаги и пыли, а также выполняет вспомогательные функции:
- охлаждает кромки детали, не допускает искусственного «закаливания» краёв;
- предотвращает тепловые деформации даже тонкого листа стали;
- защищает оптическую головку от возможных повреждений раскалёнными частицами металла;
- обеспечивает экзотермическую реакцию, делает процесс резки быстрым и точным.
При лазерном раскрое металла используются различные газы, в том числе и инертные. Выбор конкретной среды зависит от типа сплава, условий производства и производительности оборудования.
Плазмообразующий газ
Плазмообразующие газы представляют собой поток ионизированного газа. Его температура в процессе резки может достигать 15 000° С. Лазерная резка выполняется сжатой струёй плазмы. Плазма генерируется в дросселированном канале сопла режущей головки, стабилизируется с помощью системы жидкостного охлаждения.
К плазмообразующих газам PG относятся все газы, способные создать поток плазмы. К ним относятся:
- азот;
- водород;
- гелий;
- аргон.
Самым высоким коэффициентом теплопроводности обладает азот. Параметр составляет около 25,1 Вт/(м×К). Именно поэтому его чаще всего используют в плазменной резке.
Отдельно стоит отметить, что увеличение рабочего давления никак не отражается на качестве резки. Наоборот, оно может вызвать снижение теплосодержания. Объём энергии, т.е. «энтальпия» струи плазмы, зависит только объёмного расхода азота.

Режущий газ
К режущим газам SG относятся:
- Ar-H2-N2 – смесь аргона с водородом и азотом. Атмосфера в зоне резки создаётся благодаря диффузии очищенного азота, водорода и аммиака. В качестве режущего газа часто применяется сжиженный азот, который приобретет газообразное состояние в испарителе;
- Ar-N2 – смесь аргона и азота;
- Ar-H2 – смесь аргона и водорода.
Важное требование к режущим газам – необходимость дополнительной осушки перед подачей в зону резки. В этих целях используются специальные осушители с силикагелевым наполнителем.
Оборудование, использующее режущие газы SG имеет сложную фильтрационную установку и блоки осушителей. К тому же, силикагель необходимо менять минимум один раз в месяц при интенсивной эксплуатации станка.
Вихревой газ
Полезное свойство вихревых газов WG реализуется благодаря эффекту Ранка-Хилша. В результате газодинамического процесса происходит перераспределение температуры в зоне резки, турбулентный поток газа высокого давления защищает лазерный луч в зоне плавления металла. В качестве вихревого газа чаще всего применяется кислород. Его объёмное содержание не должно быть ниже 99,9 %. Кислород подаётся в зону резки через специальное сопло, имеющее вихревые каналы.
Качество резки напрямую зависит от фокусного расстояния между головкой и поверхностью металла. Отличительная особенность вихревых газов – стабильная интенсивность потока. Пучок кислорода сохраняет свою энергию даже при скачкообразном изменении «фокуса», что особенно важно при резке неровных поверхностей.
Маркировочные газы
Лазерная резка металла – это не только придание необходимой формы изделию. Она также включает в себя маркировку и удаление швов точечной сварки. Современные станки обеспечивают стабильный выходной ток в широком диапазоне регулировок. При работе с тонкими металлами лазерная головка «сужает» направленный поток ионов, чтобы исключить температурное повреждение металла.
При маркировке тонких металлов используются газы с низким давлением и скоростью потока. Резка осуществляется струёй малой плотности. Сплав не успевает перегреться, поэтому риск повреждения будущей детали практически равен нулю.
Маркировка с помощью газа используется для нанесения обозначений номера партии, даты выпуска изделия, порядкового номера предприятия-изготовителя. Использование маркировочных газов зависит лишь от того, должен или нет потребитель видеть специальные обозначения на готовом продукте.
- светлая маркировка на нержавеющих сталях производится с помощью кислорода;
- тёмная маркировка на чугунах и легированных сталях выполняется при помощи аргона.
Маркировка не является автоматизированной задачей. Оператор станка с ЧПУ для лазерной обработки металла может нанести её и вручную, к примеру, обозначив партию изделий на первой заготовке.
Выбор газа для резки металла
Для лазерной и плазменной резки сталей различной плотности применяются разные газы:
- Кислород в качестве плазмообразующего газа и смесь кислорода с азотом в качестве вихревого газа используются для обработки конструкционных сталей. Это позволяет добиться гладких кромок;
- Для легированных сталей используется смесь аргона с водородом в качестве «плазмы» и чистый азот в качестве защитного вихревого газа. Такие компоненты востребованы при резке заготовок толщиной до 6 мм;
- Для алюминия чаще применяется воздух в качестве режущего газа и азот в качестве «вихревой» защиты.
Грамотный подбор баланса газов – залог удачного исхода операции по созданию изделия. Даже самое дорогостоящее оборудование не способно самостоятельно выбирать нужные пропорции и смеси. Только большой опыт работы в сфере металлообработки и квалификация обслуживающего персонала гарантируют высокое качество продукции.
Компания PLAZMA SPB предлагает услуги по лазерной резке металла на новейших станках с ЧПУ. Мы выполняем резку черновой стали, алюминия, меди, чугуна, латуни. Срок исполнения заказа минимальный и не зависит от загруженности производства.
Оставляйте заявку прямо сейчас и получите подробную консультацию с расчетом стоимости проекта от раскроя металла до монтажа готовой конструкции
Оставить заявку